Aker Arctic has completed the hull form and contributed to the concept development for Canada’s sixteen new Multi-Purpose Vessels
The Canadian Coast Guard has a diverse but ageing fleet, with many kinds of ships for various missions built in the 1970s and 1980s. As part of the National Shipbuilding Strategy (NSS), a fleet renewal programme has been initiated with the target of replacing existing icebreakers, buoy tenders, fisheries research, and oceanographic science vessels while rationalizing the number of different classes of ships.
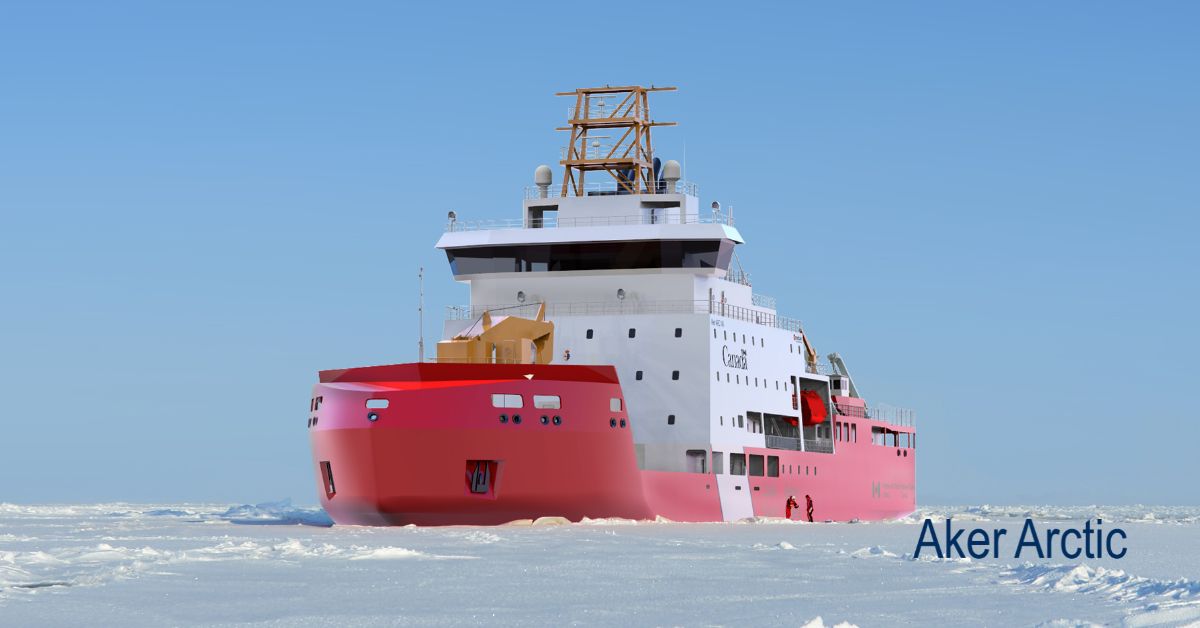
Seaspan Shipyards is responsible for delivering the non-combatant vessels being built under the NSS. The Multi-Purpose Vessel (MPV) is a key part of this portfolio.
A multitude of tasks
The MPV is replacing up to three classes of older ships with one platform. The target is to develop a compact ship with a multitude of operational roles. The sixteen vessels will mainly replace the Type 1100 class built in the late 70s and early 80s, often called the “work horses” of the fleet, doing the day-to-day work of supporting shipping by maintaining fairways, aids to navigation, and icebreaking.
The MPVs will also perform cargo missions, bringing supplies to northern communities, carry out search & rescue and patrol missions, in addition to icebreaking. Most of their time will be spent on the St Lawrence River, the Great Lakes, and along the Canadian East Coast. Additionally, they will have a summer Arctic mission leaving from Victoria in British Columbia and travelling north around Alaska to the Canadian Arctic.
Due to the wide variety of tasks, the long-distance mission to the western Arctic, and the fact that some of the waterways have a limited depth, the vessel needed to be compact with a shallow draught, narrow beam, high endurance, and with a large cargo capacity.
Collaboration from the start
Contrary to many other governmental projects, the Coast Guard opted for a collaborative model which involved the owner and operator, the shipyard, and the designer working jointly on creating the concept from day one.
“This method has proven efficient and fruitful, as all the shipyard’s learnings from previous builds for the customer have been possible to implement at an early stage,” says project manager Rob Hindley, team leader, Structural Design at Aker Arctic.
“It also ensured that the overall parameters, i.e. hull form, size, main dimensions and main powering are validated, forming a basis which the shipyard can further refine and build.”
Mutual understanding
The Coast Guard had a clear idea of their needs and wanted assurance that the main dimensions, volume and shape of the hull were suitable for fitting everything needed.
“They conveyed their desires efficiently which ensured a mutual understanding of what they wanted from the beginning. The design process included balancing priorities and what could be fitted in. Furthermore, the shipyard gave valuable input on limitations in construction work, so that we did not add in any features which would be impossible to build,” Hindley underlines.
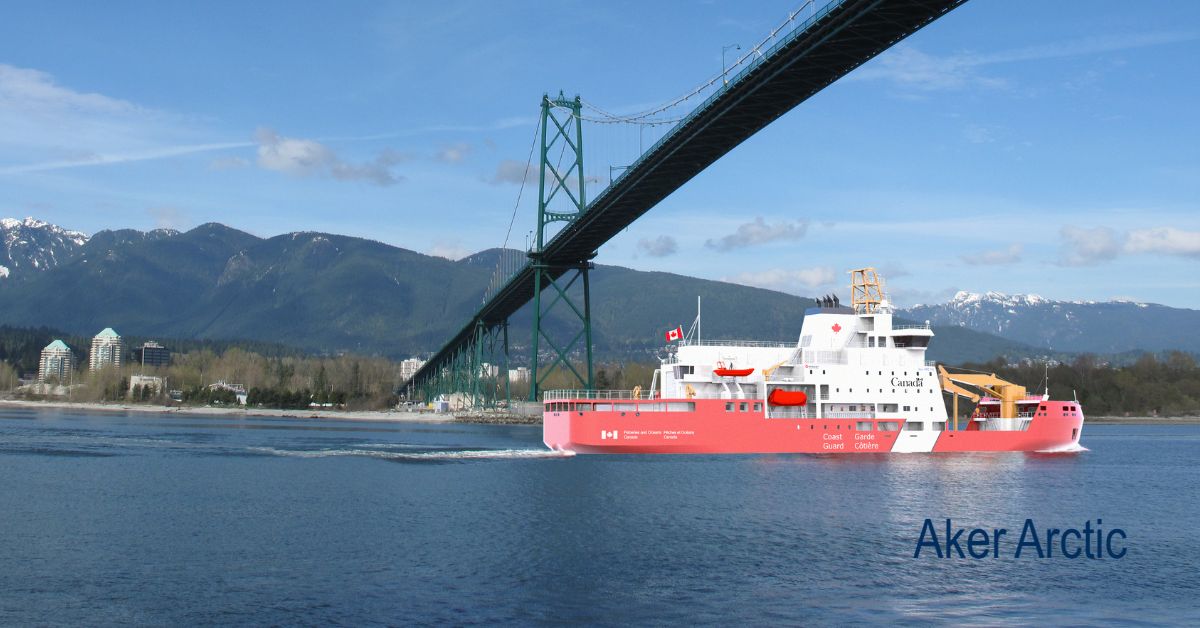
Aker Arctic’s aspiration was to develop a concept design with a hull form which balanced icebreaking, seakeeping and open water performance, and was compact yet big enough to accommodate everything.
“As part of developing the hull form, we needed to demonstrate that the envelope allowed the ship to achieve its planned missions,” Hindley says.
The end result is a hull form which has had its performance confirmed through ice model testing. Aker Arctic has also provided the design documentation which the shipyard now takes into the functional design phase, developing the design details and approving it by the classification society.
Weekly meetings
The collaboration has required frequent communication and sharing of knowledge. To enable an efficient flow of design information Aker Arctic held online weekly meetings with Seaspan and the Coast Guard, regardless of time differences.
“It has been key to the success of this project,” Hindley emphasizes. “The effort to keep the coordination going paid off as we understood at all times what the owner and operator wanted and could develop the solution together.”
Optimisation of the design
During the design process a need arose to evaluate the future environmental impact and greenhouse gas emissions, bearing in mind that this is a long-term project.
In the end, the Coast Guard decided to update the design with an optimized version, where the ship was redesigned to allow for future alterations when alternative fuels become available. For this, new calculations were made on the impacts of a future lengthening on stability and weight.
“We also anticipated what the ice loads would be if the ship’s displacement is increased and designed a hull which is stronger to allow for a mid-life modification,” Hindley says.
“Although every aspect was not possible to anticipate, we managed to design a hull form that meets the Coast Guard’s requirements of performance, is as compact as possible, and has a provision for future modifications built into the design.”
Learnings from the evaluation
A number of energy-saving devices were also evaluated. These included energy-storage devices such as battery packs; thermal storage in the form of waste heat utilisers capturing and reusing heat from the power plant; and alternative energy sources such as energy stabilizers, solar panels and wind turbines.
The aim was to evaluate the present state of the technology and how practical it would be to implement it into the design for optimal environmental efficiency.
Due to the ship’s size, a decision was made to prioritize the missions against using space for energy-saving devices at this stage. However, as the design continues to progress and spaces and weights become finalized, there is the possibility of implementing some of the options.
As Seaspan Shipyards now progresses towards the functional design work, Aker Arctic continues to support Seaspan particularly on the hull and performance aspects to ensure that everything meets the requirements set out by the Coast Guard.
General information about Aker ARC 146: | |
Length over all | 99.9 m |
Beam | 20.3 m |
Design Draught | 6.2 m |
Displacement | about 8500 tons |
Propulsion | diesel-electric; two azimuthing propulsion units |
Ice class | Polar Class 4 |
Source: Aker Arctic